Summary
The Ontario Workers Health & Safety Training Centre provides training on Indoor Air Quality. It’s valuable training for Joint Health and Safety Committee members to provide them on background to better understand how to go about gathering and analyzing information on indoor air in the workplace. The training covers common issues, limitations, and responsibilities. (preview here) Given the importance of indoor air quality, how JHSC members might not have formal training and possible reluctance of the employer to address poor indoor air, this kind of training is vital for workers to take.
Background
In December I undertook the Air Quality Training session by WHSC, along with another member of our faculty association, and an employee of the University’s Health Safety and Employee Well-Being department. The HSEWB employee acts as an advisor on multiple JHSCs and has access to the same source notes that I have and which formed the basis for this blog post.
After the training, I posted some notes on Twitter, but this blog post expands on my observations from the training. It was really insightful and confirmed what I had suspected: that workers have the right to know about air quality and air quality infrastructure. We breathe 14 kg of air per day. That's a lot of air. And if we're working 8 hours a day indoors then our employer is responsible for just over 4 kg of air per employee over the course of the work day -- it needs to be safe to breathe.
If you’re not familiar with what JHSCs do or how they work, the City of Toronto has a straight-forward guide for its JHSCs that is worthwhile consulting.
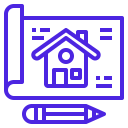
Key Take-Aways
Key take-aways from the WHSC training on Indoor Air Quality:
- JHSCs, including non-expert members, have the right to information on how the HVAC system operates (see pgs. 19, 21), including:
- Designs (e.g. plans, layouts, components, “blueprints”, etc.)
- Operational information (e.g. control settings, schedules for temperature values, etc.)
- Interviews with HVAC maintenance workers
- Non-expert workers can take measurements of aspects of air quality, including temperature, humidity, carbon monoxide, carbon dioxide and expect reports to be taken seriously by the employer.
- Sections 9 and 25 of the Occupational Health and Safety Act (the “Joint health and safety committee” and “Duties of employers” sections) are especially important for JHSC members to know about.
- Workers, including JHSC worker members, are entitled to engage in “workplace monitoring” of air quality as part of the hazard assessment process (pg. 27, 28). Worker members are entitled to be present during occupational hygiene testing.
- Engaging in measurements is not the goal. Eliminating hazards is the goal. (pg 28) And when elimination is not possible, then control of the hazard is necessary (pg 41).
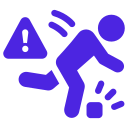
Without measurement you can't control hazards
This last point among the key take-aways above is important. Measurement is means to an end. Once it is established that a hazard cannot be eliminated, the goal becomes to control the remaining hazards. Measurements and observations are means to controlling those hazards. If you are prevented from measuring or observing a hazard or its mitigation processes then you cannot eliminate or control it.
Neither workers nor employers should want JHSCs to spend an inordinate amount of time measuring temperature, CO2 levels and ventilation rates in the workplace. Ideally, JHSC workers wouldn’t have to do it at all because the HVAC system would run perfectly and sufficiently. But studies point to the “the HVAC system itself as the source of 40 to 50 pers cent of problems experienced.” (pg. 27)
And, so, our workplaces have hazards in them, from the photocopier spewing VOCs to the staff member sick with an airborne-transmissible virus. If the ventilation system is operating at a low level either intentionally (to save money) or unintentionally (broken parts), then the hazard path is compromised.
Workers must be permitted to conduct measurements and observations of hazards or hazard paths. They must also be allowed to view current and historical data about these measurements and hazards.
Strategies for IAQ Control
According to the CCOHS there are six recommended strategies for controlling indoor air quality:
- Source management. Ex: if carpets are releasing VOCs, remove or replace them.
- Local exhaust. Ex: fume hoods in a lab.
- Ventilation. Ex: Clean, filtered air from the outside, brought in through the HVAC system.
- Exposure control. Ex. Apply pest control poison on weekends when the building is unoccupied.
- Air cleaning. Ex. Use HEPA filter air cleaners in a classroom.
- Education. Ex. Talk to workers about hazards and the “operation of the ventilation system.”
Obtaining Records for the JHSC
Eliminating hazards in the workplace is the goal of a JHSC. To do so, JHSCs must engage in the gathering and analyzing of relevant information. This requires that the employer act in an open and transparent manner about records, including those associated with HVAC design and operation. (pg 19)
On page 19 of the document (section “Obtaining Records”) the WHSC authors are unequivocal on the “right [of the JHSC members] to obtain health and safety records…” including those that “detail the construction and operation of the building.” This is considered important for the JHSC to “evaluate the effectiveness of any controls that exist”.
Again, the JHSCs have the right to know about the design of the building, as well as its current operation. That means that the employer needs to make related documents and electronic reports available. There are precedents for this, as such elements were provided to external consultant CFMS when it undertook an examination of air quality systems at York.
Page 61 of the WHSC document contains a “HVAC and building inspection survey” resource sheet. JHSCs should be able to fill out this form as part of their inspection duties, likely with the aid of non-JHSC workers who have expertise to the design, operation and maintenance of the HVAC systems. This resource sheet triggered questions from one attendee about a scenario where the employer refused to provide information for this survey. The response from our instructor was that the OHS Act requires that the employer cooperate with the committee on providing HVAC information.
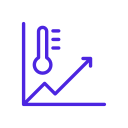
Our instructor made it clear that it is reasonable for the JHSC to request HVAC information and that it is reasonable to assume that the employer will provide it. Furthermore, our instructor made it clear that if the employer refuses to divulge HVAC information to the committee after a 21-day Recommendation then it is also reasonable for the JHSC to reach out to the Ministry of Labour to “direct the employer to provide that information.”
The discussion continued regarding an employer who claimed an inability to provide HVAC information and our instructor responded with “reach out to third parties” like industrial hygienists at OHCOW or “fee for service” entities like Pinchin.
Another question was raised as to where “access to ventilation systems” fell within the JHSC responsibilities. Our trainer was clear: yes, such information falls within the JHSC mandate and that the JHSCs can request information on ventilation systems from the employer. Our instructor even provided suggested wording:
“we want to ascertain the health of our heating ventilation and air conditioning system to address the health and safety concerns raised by workers.”
WHSC Instructor recommendation for requesting information on the HVAC systems from the employer
The employer should then provide that information to the JHSC so that the JHSC can then use that information to feed its analysis and recommendation process. In fact, this can all be wrapped into a recommendation framed along the lines of:
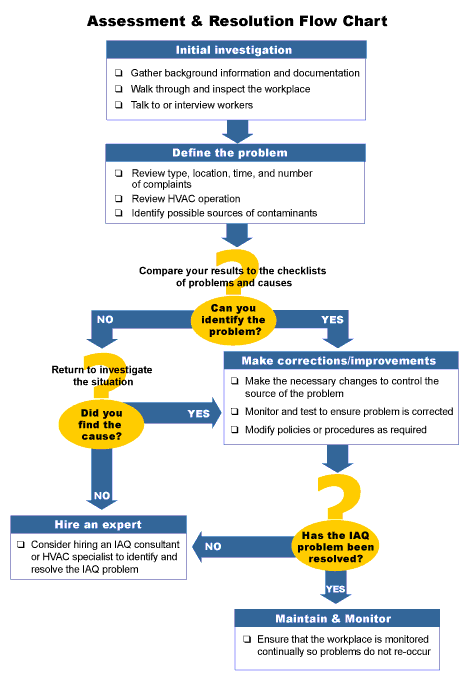
- We request that the employer conduct a “health of the HVAC” study and,
- Based on the study, update the HVAC so that it no longer causes X, Y and Z issues.
But, at the end of the day, health and safety concerns must be addressed and, if the employer refuses to do so then the Ministry of Labour should be called in to “for lack of a better term, “adjudicate” and “potentially order the employer… to provide the information” and to describe a plan for fixing the concerns.
Visualization for assessing and resolving indoor air quality issues
The CCOHS has a useful summary flowchart that aligns with the training document from WHSC, in particular the one on page 65 of the WHSC document. You can find the CCOHS flowchart here.
Two key points from the CCOHS flow chart and from the WHSC training documents are:
- The workplace needs to be “monitored continually”. That requires observation and measurement.
- If you can’t resolve the problem, then consider “hiring an IAQ consultant or HVAC specialist” (from the outside).
The JHSCs are not expected, and likely don’t have the expertise or access to be able to directly execute on all elements of these flowcharts, but can be involved especially by using them for analyses.
Measurement of Carbon Dioxide
Note, in the CCOHS flowchart above, the need for "Review HVAC operation" and "Monitor and test" bullet points. Measuring of air quality make up important elements of both of these. Carbon Dioxide measurement is one of the key aspects that needs to be assessed when assessing air quality in the workplace.
Unfortunately, CO2 monitoring is one the most contentious topics in the health and safety context at York University in recent years. An external consultant work revealed that many CO2 sensors operated by the University were likely broken or had lost calibration. Given this and given the admission that the "Facilities [Services Department] is not equipped to monitor [the air quality of] all indoor spaces at all times" (HSEC minutes, Item 2211-01, May 2023) one would think that it would make sense to provide equipment and training to workers to report air quality measurements back to the employer. Instead, we get webpages from the employer discouraging it.
That said, both the WHSC training document and Appendix A of York University’s Air Quality Program agree that 1000ppm of carbon dioxide indoors is a threshold of concern that the indoor air may be “under-ventilated” pg. 30. That’s for an instant of time, not on average. Studies have shown that short-term exposure to CO2 levels above 1000ppm have an effect on cognitive performance.
There are caveats and contextual issues, as described on pages 27 – 30 of the training document. For instance, it’s important that the measurements be taken multiple times and that the context be established, including “number of people in the building, air damper settings and weather.” (pg. 30)
The WHSC training session and documentation is clear: non-expert workers can and should use measurement devices to evaluate indoor air quality. For example, workers can use a thermometer to measure indoor temperature and report when it’s too hot or too cold. The same applies for CO2 measurement.
But the measurements of elements of indoor air quality like carbon dioxide should not end with non-expert workers. The JHSCs and the employer should strive to use that information to inform expert data gathering to ensure either the elimination of a hazard or a properly controlled hazard path. And it should be assumed that monitoring and reporting will continue because internal and external factors are dynamic.
Conclusion
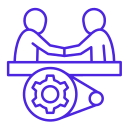
This was a valuable training session on an important topic, indoor air quality. It's clear that JHSCs have the right to access HVAC and air quality data and that the employer should cooperate to:
- assist JHSCs to evaluate air quality and identify air-quality-related hazards,
- provide JHSCs with information on air quality and air quality infrastructure, and
- eliminate or control air quality hazards openly and transparently.
The instructor during this session made it clear that even non-experts can be involved in this process. Worker observations and measurements, in spite of their limits, should be taken seriously. Finally, it was made clear that the Ministry of Labour should be called in if the employer does not provide information requested by JHSCs or does not follow-through on JHSC recommendations that seek to eliminate or control air quality hazards.
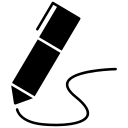
James Andrew Smith is a Professional Engineer and Associate Professor in the Electrical Engineering and Computer Science Department of York University's Lassonde School, with degrees in Electrical and Mechanical Engineering from the University of Alberta and McGill University. Previously a program director in biomedical engineering, his research background spans robotics, locomotion, human birth and engineering education. While on sabbatical in 2018-19 with his wife and kids he lived in Strasbourg, France and he taught at the INSA Strasbourg and Hochschule Karlsruhe and wrote about his personal and professional perspectives. James is a proponent of using social media to advocate for justice, equity, diversity and inclusion as well as evidence-based applications of research in the public sphere. You can find him on Twitter. Originally from Québec City, he now lives in Toronto, Canada.
Icons on this page are used under licence from The Noun Project.
Edit History
January 20, 2024: tags added to the blog post.
January 25, 2024: bullet point shapes cleaned up. Measurements section added to provide structure to existing information after the key aways section. Additional paragraph added there. Two paragraphs added to the CO2 section, with links to HSEC, Facilities and external consultant report evaluations.